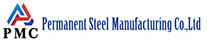
Como elemento fundamental en el sector industrial, la vida útil de las tuberías de acero al carbono está directamente relacionada con la eficiencia operativa y el coste de seguridad de los equipos. A continuación, se analizan los principales factores que influyen en las dimensiones de los materiales, el entorno, las condiciones de trabajo, etc., y se ofrecen soluciones específicas.
Selección de materiales: los genes innatos determinan el límite superior de la esperanza de vida
1. Diferencia en el grado del acero
Q235B: Acero al carbono común, con baja resistencia a la corrosión, su vida útil suele ser de 5 a 8 años (en ambiente seco normal).
Q345B: Acero de baja aleación, con una resistencia aumentada en un 30% y una mayor resistencia a la corrosión atmosférica.
Acero corten (como Q355NH): Al añadir elementos de aleación como cobre y níquel, su vida útil en exteriores puede superar los 15 años.
2. Proceso de tratamiento térmico
El tratamiento de normalización puede refinar los granos y mejorar la resistencia a la fatiga; el tratamiento de temple y revenido equilibra la resistencia y la tenacidad, lo que lo hace adecuado para entornos de alta presión.
El tratamiento de temple y revenido es una combinación de temple y revenido a alta temperatura, que permite lograr un buen equilibrio entre la resistencia y la tenacidad de la tubería de acero y un mejor rendimiento general.
Ambiente corrosivo
1. Erosión por medios químicos
Entornos ácidos (como ácido sulfúrico o ácido clorhídrico): causan corrosión uniforme, con una tasa de pérdida anual de entre 0,5 y 2 mm.
Entornos con iones cloruro (océano, niebla salina): inducen corrosión por picaduras, con un alto riesgo de perforación.
Entornos alcalinos: La tasa de corrosión es baja, pero es fácil causar grietas por corrosión bajo tensión.
2. Corrosión electroquímica
El contacto entre metales diferentes (como acero al carbono y acero inoxidable) forma microbaterías que aceleran la corrosión del ánodo.
3. Corrosión por influencia microbiológica
Las bacterias reductoras de sulfato se multiplican en entornos con deficiencia de oxígeno, causando corrosión localizada de tipo ulcerativo. Estas áreas de corrosión se expandirán gradualmente, afectando gravemente la resistencia estructural y la vida útil de la tubería.
Condiciones de trabajo: lesiones mortales por sobrecarga
1. Presión y temperatura extremas
El funcionamiento prolongado con sobrepresión (> 1,2 veces la presión nominal) provoca deformación plástica de la tubería; las altas temperaturas (> 350 °C) aceleran la eliminación de óxido y generan corrosión en las ranuras.
2. Desgaste por erosión de fluidos
Los fluidos de alta velocidad (como vapor o líquidos con partículas) erosionan los codos y las válvulas, lo que reduce el espesor de las paredes y la tasa de desgaste puede alcanzar de 0,1 a 0,3 mm/año.
Instalación y mantenimiento: la regla salvadora del mantenimiento adquirido
1. Defectos de soldadura
Defectos como la penetración incompleta y las inclusiones de escoria pueden convertirse fácilmente en el punto de partida de la corrosión y deben inspeccionarse exhaustivamente mediante pruebas ultrasónicas.
2. Daños en la capa anticorrosiva
Un espesor insuficiente de la capa galvanizada (<85 μm) o defectos de poros en el recubrimiento epóxico provocan oxidación local.
3. Mantenimiento tardío
Si no se inspecciona regularmente el espesor de la pared (recomendado cada 2 años), se perderá el mejor momento para la reparación.
Estrés ambiental y daño mecánico externo
Estrés del suelo
El asentamiento desigual provoca una tensión de flexión concentrada en las tuberías, lo que reduce la vida útil por fatiga en más de un 50 %.
Expansión y contracción térmica
Cuando la diferencia de temperatura supera los 50 °C, la falta de instalación de juntas de expansión puede provocar fácilmente fugas en la interfaz.
Daños en la construcción: Las colisiones de izaje causan abolladuras, que se convierten en una fuente de corrosión.
Daños a terceros: Las excavaciones provocan perforaciones en las tuberías, y el costo de la reparación representa el 30 % de la pérdida total.
Soluciones integrales para prolongar la vida
Mejora del material: elija entre tubería compuesta con revestimiento de acero corten o acero inoxidable.
Refuerzo anticorrosivo: utilice revestimiento 3PE (espesor ≥ 2,5 mm) + protección catódica.
Monitoreo inteligente: instale sensores de corrosión en línea para obtener alertas en tiempo real.
Diseño flexible: incorpore casquillos resistentes al desgaste en los codos para reducir las pérdidas por erosión.
La vida útil de las tuberías de acero al carbono es el resultado de la interacción entre las propiedades del material, la erosión ambiental y la gestión de la operación y el mantenimiento. Mediante una selección precisa de materiales, un tratamiento anticorrosivo científico y un mantenimiento activo, la vida útil puede extenderse del promedio de la industria de 8 a 10 años a 15 a 20 años, logrando el mejor costo de todo el ciclo de vida.
Leer más: ¿Cómo almacenar tubos de acero al carbono?