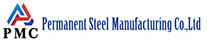
Common materials and characteristics
Stainless steel elbow is a pipe fitting used to connect two pipes with the same or different nominal diameters in a piping system to make the pipe turn at a certain angle.
1. 304 stainless steel elbows have good corrosion resistance, heat resistance and mechanical properties, and are widely used in general industrial pipelines and civil building pipeline systems. They are relatively moderately priced, cost-effective, and can meet the use requirements of most conventional environments.
2. 316 stainless steel elbows are made by adding molybdenum to 304 stainless steel to further improve its corrosion resistance. They perform well in environments containing highly corrosive media such as chloride ions. They are often used in chemical, marine engineering, pharmaceutical and other fields that require high corrosion resistance.
3. 316L stainless steel elbow, 316L is ultra-low carbon stainless steel with lower carbon content. It is not easy to produce intergranular corrosion during welding. The welding performance is better than 316 stainless steel. It is suitable for occasions with high requirements on welding quality, such as food processing, medical equipment and other industries. It can ensure the safety and stability of the pipeline system during long-term use.
Connection methods of stainless steel elbows
In industrial piping systems, stainless steel elbows are widely used due to their good corrosion resistance and durability. In order to adapt to different installation requirements and working environments, stainless steel elbows provide a variety of connection methods, including welding, threaded connection and flange connection. These connection methods not only ensure the sealing and reliability of the piping system, but also provide flexible and diverse installation options.
1. Stainless steel elbows welding connection:
Welding is one of the common connection methods for stainless steel elbows. By welding the elbow directly to the pipe, a high-strength and high-tightness connection can be achieved. Welding connections are suitable for high pressure and high temperature applications and can withstand large mechanical and thermal stresses. Welding methods commonly include TIG (Tungsten Inert Gas) and MIG (Metal Inert Gas), both of which provide good quality weld joints. The advantages of welding connection are compact structure and no risk of leakage, but it requires dedicated welding technology and equipment.
2. Stainless steel elbows threaded connection:
Threaded connection is a quick and easy way to connect. The stainless steel elbow is pre-processed with internal or external threads, which can be connected to the pipe with corresponding threads by tightening. This connection method is suitable for low-pressure and small-diameter piping systems, and is particularly suitable for occasions that require frequent disassembly and maintenance. The advantages of threaded connection are simple operation and no need for special tools, but its sealing performance depends on the quality of the thread and the choice of sealing material.
3. Stainless steel elbows flange connection:
Flange connection is a widely used connection method, especially in large-diameter and high-pressure pipeline systems. The stainless steel elbow is equipped with flanges at both ends, and the elbow is connected to the pipe or other flange parts by bolts and gaskets. The flange connection has high sealing and disassembly properties, making it easy to install and maintain. The advantages of flange connection are stable structure, reliable sealing, and can be inspected and repaired without damaging the pipeline. Common flange types include flat welding flanges, butt welding flanges and loose flanges.
Read more: Seamless Welding Technology of Stainless Steel Elbows